Crafting sustainability within jewelry and metal arts
The °®¶ą´«Ă˝ community of jewelers and metalsmiths are at the forefront of pushing their industry forward to a more ethical and responsible future.
°ä°ä´ˇâ€™s Jewelry and Metal Arts program is more than a century old. Founded in 1912, it’s one of the longest-running programs of its kind. Indeed these students work within a craft that is one of humanity’s most ancient.
Yet, in the recent past jewelry makers and metalsmiths have contended with issues of sustainability and environmental impact. Where can we responsibly source our metals and materials? How can we better recycle? What’s the environmental impact of the chemicals we use in the studio?
Questions like these are at the heart of the °®¶ą´«Ă˝ Jewelry and Metal Arts program’s efforts to make their practice more socially and environmentally responsible.
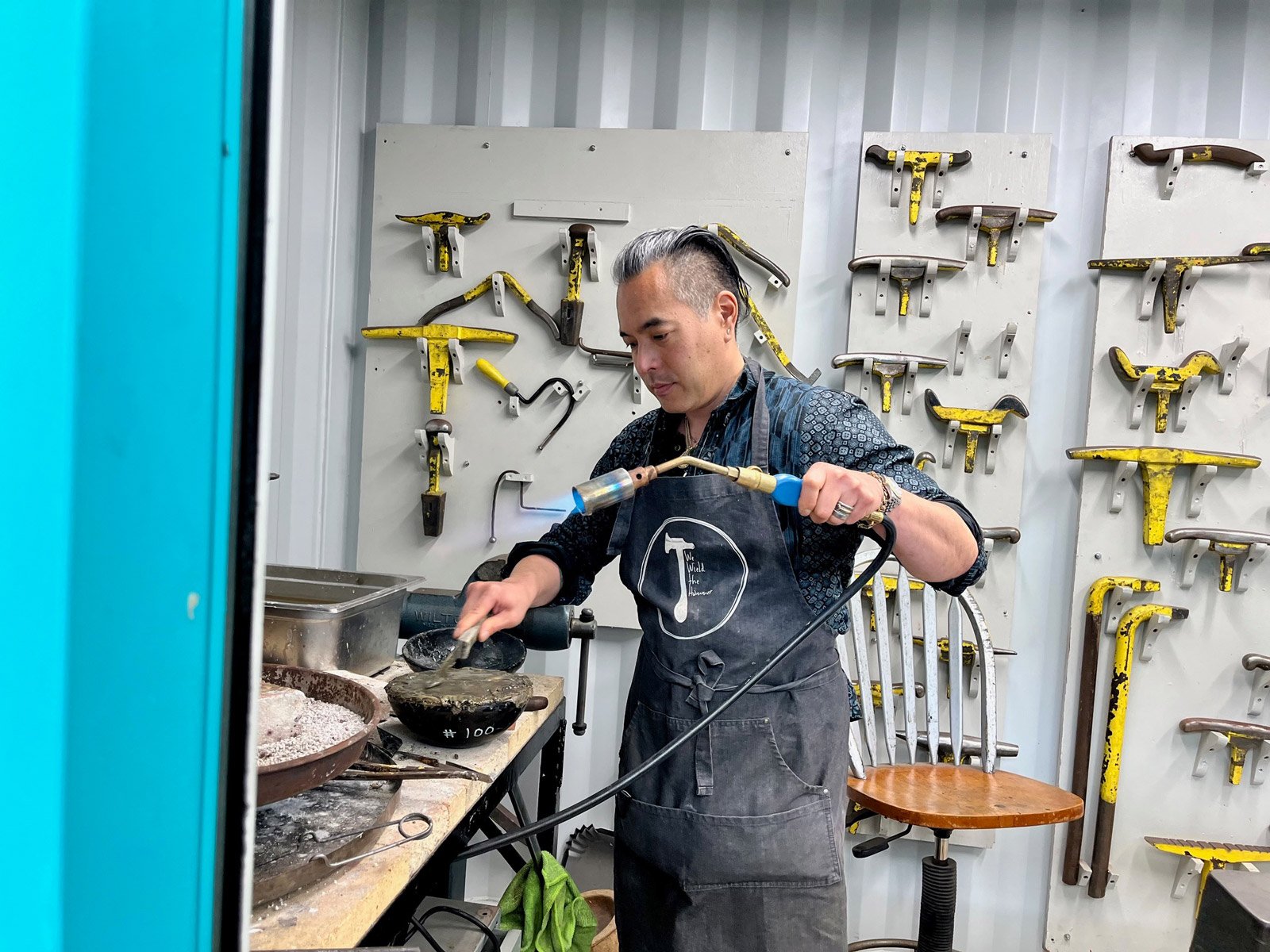
Chair of Jewelry and Metal Arts Curtis Hidemasa Arima gives a demonstration on preparing a pitch for chasing and repoussé.
Curtis Hidemasa Arima, chair of Jewelry and Metal Arts, and Russell Larman, studio manager for Jewelry and Metal Arts are leading these efforts at °®¶ą´«Ă˝ and beyond. (Arima was recently voted to the board of directors of the organization.)
“We’re basing our sustainability tenets for the whole program with environmental sustainability running through all of it,” says Arima. “That's the driving force for the program, from how we make decisions for curriculum and operations to what techniques we teach and what materials we allow students to use.”
This holistic mindset means that students learn about environmental justice issues related to large-scale mining. They learn how to creatively recycle metals and alloy their own. They use safer and more people friendly practices in the studio. And they learn the most innovative tools used in their industry.
“Even if some concepts and practices around sustainability or social justice aren’t necessarily relevant for a particular student or their work, we bake these core tenets into the program so they only learn how to make with sustainable or ethical methods,” says Larman.
Giving discarded materials new life
One of the large questions for jewelers and metalsmiths who want to make the industry more ethical is where to source the metals they need to craft their pieces.
Larman explains that many raw sources of metal come from large-scale corporate mines that often destroy whole landscapes and contaminate groundwater. “The jewelry industry is one of the largest consumers of gold and platinum and other precious metals,” he says.
Larman and Arima have looked to source metal from ethical operations, which are small-scale and conform to strict labor and environmental standards. But these can have challenges of their own depending on the type of teaching materials the program needs.
If you browse through the metal scrap bin, you can find usable bits or forgotten projects. I did a big casting project where instead of buying fresh casting grain, I used what I found to make my own bronze.”
So the jewelry and metal arts community at °®¶ą´«Ă˝ recycles just about everything. And it’s one of the simplest yet most ingenious ways they’re making their craft more sustainable. Arima, for instance, has been teaching students how to alloy bronze as well as a Japanese alloy called shibuichi, from recycled copper.
Coli Drechsel, a Jewelry and Metal Arts student whose own practice emphasizes nature and the environment, explains how they close the loop by making discarded materials anew.
“If you browse through the metal scrap bin, you can find usable bits or forgotten projects,” Drechsel says. “I did a big casting project where instead of buying fresh casting grain, I used what I found to make my own bronze.”
Students also cross disciplines and mediums to creatively adapt materials for their projects. Jewelry and Metal Arts student Posy DiPaolo also works in ceramics and explains how she incorporates discarded glaze into her pieces.
“Glaze is often a waste that drips off of ceramics,” she says. “But I can make these beautiful caps that resemble gemstones. Normally these things would be thrown away, but I put them in my work.”
Placing people and safety at the center
Although students can creatively and confidently recycle metals for their projects, the question of locating metals that are ethically sourced remains a priority for Arima and Larman.
For certain types of metals they’ve been able to locate vendors such as Hoover and Strong that have been certified as sustainable and with sources that are Fairmined.
“The metals we supply and which students mostly start out with in the studio are copper, brass, and nickel,” says Larman. “And recently we've been able to introduce a small amount of gold into the curriculum which came from a Fairmined source, meaning it was traced and it was produced under really strict guidelines for environmental impact and as well fair wages and labor practices.”
Arima and Larman have also instituted innovative changes that make the Jewelry and Metal Arts studio a safer place to create.
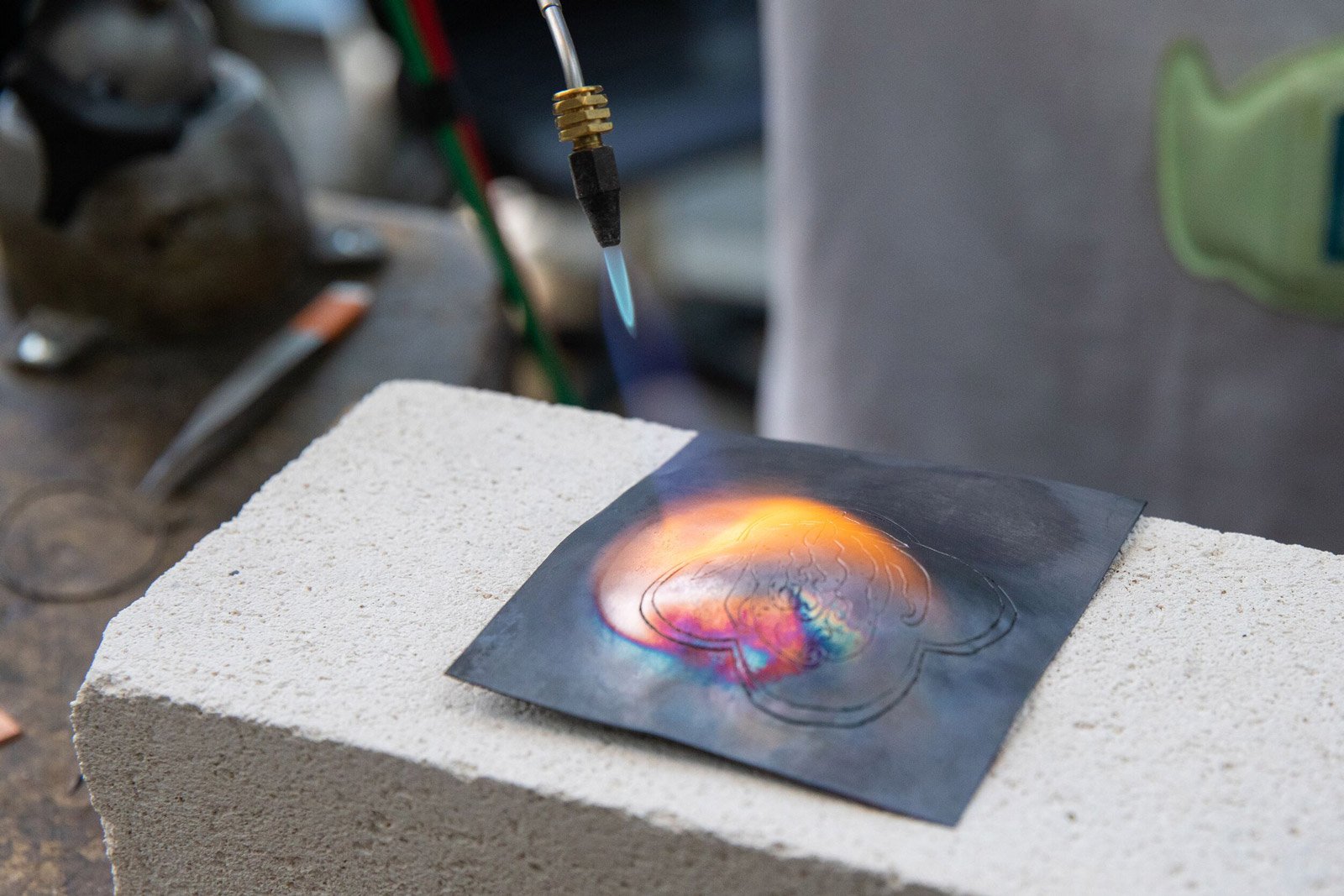
Safer and more environmentally friendly materials have replaced harmful chemicals in the studio.
One of those is the elimination of harmful acids. Arima says, “Chemicals such as ferric chloride and nitric acid were used to etch metal. And sodium bisulfate was used as a pickle solution to clean off pieces of worked metal.”
“We eliminated those,” he says. “They give off bad fumes, aren’t great to breathe, and will also literally burn you.”
Galvanic etching, which combines a mineral solution with an electrical current, has replaced ferric chloride and ferric nitrate etching. And students now use a pickle that is a mixture of 20% citric acid and 80% tap water. “Before you put the metal in you could even taste it and it would be safe,” says Coli Drechsel.
A key tool in any jeweler or metalsmith's kit are torches which are used to melt metal for casting, annealing, soldering, brazing, patination, and more.
These torches were supplied by an oxygen/acetylene tank that had to be transported and moved, but now the studio uses oxygen/natural gas from the local utility with a natural gas booster. “Acetylene is a more dangerous gas,” says Arima. “Natural gas burns cleaner than acetylene, and we eliminated having to store the tank in the studio, which makes it safer for the students overall.”
New technologies alongside traditional craft
Looking to the future, the Jewelry and Metal Arts program carries the tradition of craft forward while adding the latest innovative tools as options for students to explore. “For example, that would be 3D modeling contrasted with chasing and repoussé, which is making your own tools,” says Arima.
Coli Drechsel, for instance, has created a whole set of carefully crafted tools designed for their specific pieces. “I made stone setting tools called burnishers during my apprenticeship. And I use these tools to push metal over stones to hold them in place,” Drechsel says.
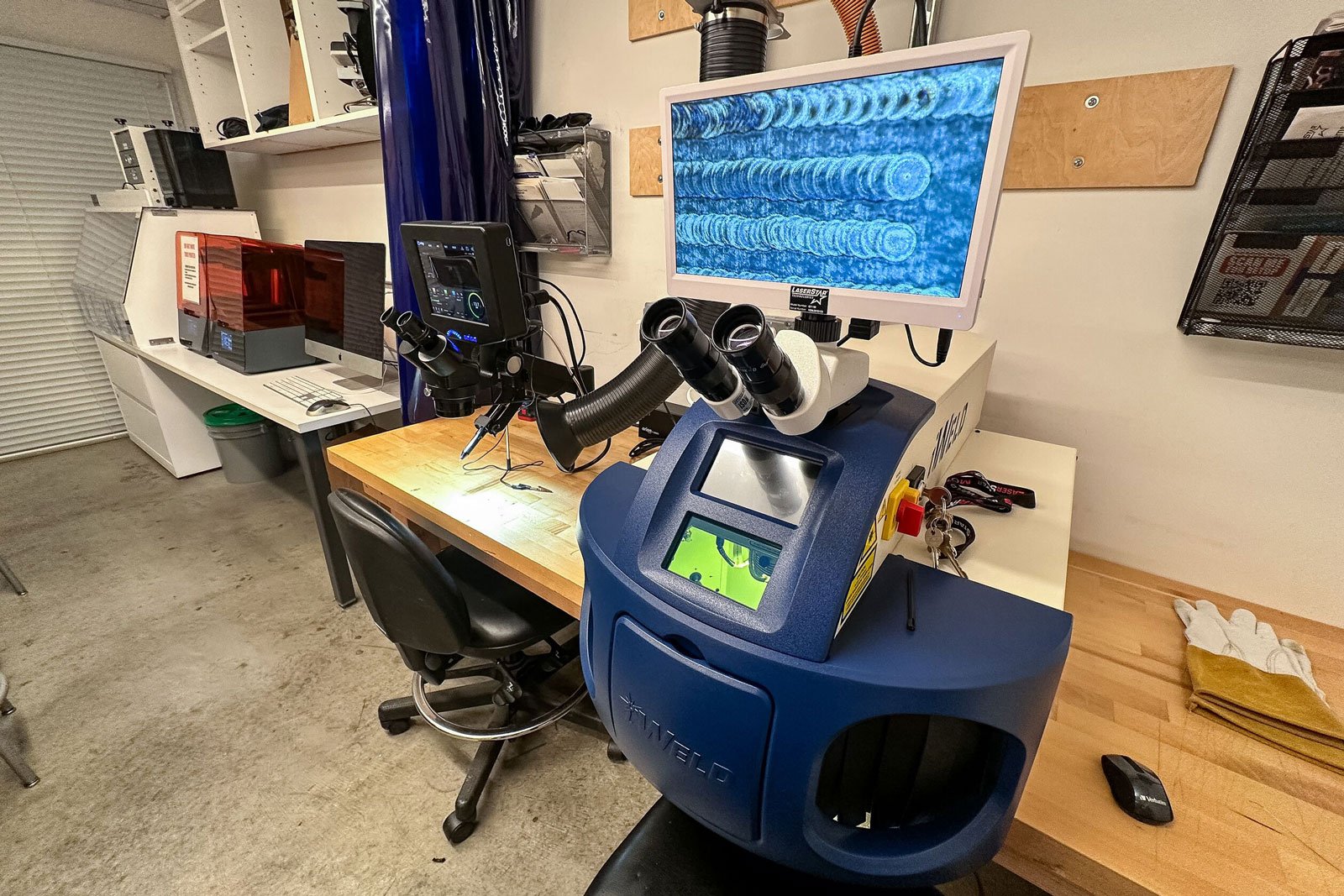
Technologies like 3D printing, laser welding, and mold injecting are used alongside traditional chasing and respoussé in the Jewelry and Metal Arts studio.
Posy DiPaolo explains how the latest technologies are incorporated into the Jewelry and Metal Arts studio. “We can use a mold injector, a 3D printer, and we are really lucky to have a laser welder, which is something that is a marketable job skill,” DiPaolo says.
Arima adds, “When new technology like a laser welder comes in, we don’t necessarily eliminate soldering, we just add it to the diversity within the curriculum alongside other sustainable practices.”
Russell explains that teaching students on new types of technology helps sustain the profession as a whole because it allows these students to both have marketable job skills but also carry what they know about sustainability into the jewelry making profession.
“New equipment like these fall directly in line with our sustainability work because it enables students employable job skills, these are tools that are more relevant now than ever in our industry,” he says.
As Drechsel considers their future as a teacher, creative, and maker, they intend to carry this knowledge they've learned from Arima and Larman to successive students learning the craft.
Drechsel says, “They are creating that next generation of metalsmiths who don't know anything else other than sustainable practices.”